ET-SC-ACP-2000 Aluminum Composite Panel(ACP) Composite Production Line
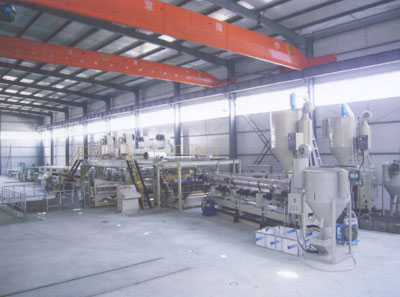
Specifications of Aluminum composite panel compound production line(SC£2000)
Major parameters of the whole line:
Item |
parameter |
quantity |
Extra information |
1.D180mm plastic extruder for PE core layer |
1)Single screw extruder with double vacuum exhausting devices; 2) Extruding capacity:1300kg/h; 3)Dimensions:L7300mm¡ÁW4200mm¡ÁH4100mm; 4)Carbon steel beam channel chassis; 5)Screw dimension:D180mm¡ÁL/D=35; 6)Screw rotating speed:65rpm; 7)Reducing rate:1:16; 8)Oil pump for cooling bearings:0.75kw¡Á1(including cooling device and the filter) 9)Temperature controlling system:8 point SCR temperature controlling system; 10)Screw heating method: cast Aluminum heaters; 11)Heating zone: 8; 12)Heating power:144.5kw; 13)Cooling method: air-blasting fan; 14)Cooling power:0.37kw¡Á8=2.96kw; 15)Main motor:220kw¡Á2; 16)Screw meters:1 set; 17)Automatic hydraulic screen-exchange device:3kw; 18)Extruder funnel capacity:750L; 19)Vacuum exhaust pump:7.5kw¡Á2; 20)Chassis-position adjusting device: reducing motor0.75kw; |
2 |
|
2.T-shape extruder mold(SC-2000-02) |
1)Adjustable scope of lip mold: 2.0mm-10.0mm;
2)Chassis material: high quality alloy;
3)Internal surface:with high quality buffing treatment and plate chrome treatment;
4)Effective space of the mold mouth:2000mm;
5)Heating method:cast Aluminum heaters;
6)Heating zone:8 areas;
7)Mold heating power:19.5kw¡Á2=39kw; |
1 |
|
3.Funnel dryer(SC-2000-03) |
1)Funnel capacity:750L;
2)Funnel raw material:high quality stainless steel;
3)Drying method:electricity heating air fan;
4)Heating power:0.75kw;
5)Electricity heating capacity:22Kw-3 phases-380V-50Hz; |
2 |
|
4.Raw material feeder(SC-2000-04) |
1)Motor power:4kw;
2)Feeding capacity:2000kg/h; |
2 |
|
5.Level-off machine for PE core layer |
1)Dimensions:L1800mm¡ÁW2010mm¡ÁH2020mm;
2)Weight:5500Kg;
3)Carbon steel chassis; Quantity of driving rollers:3 sets;
4)Roller controlling system:the middle roller is fixed;the upside and downside rollers are driven by hydraulic controlling motors;
5)Driving motors:3.0kw¡Á3;
6)Linear velocity:0.4-5.5m/min;
7)Quantity of the conveyer rollers:10sets;
8)Roller dimension:D60mm¡Á2000mm; |
1 |
|
6.Macromolecue film presetting rollers |
1)Macromolecue film holding roller:D75mm¡ÁL2000mm;
2)Quantity of the holding rollers:4 sets;
3)Macromolecue film-side high precise adjusting device:4 sets; 3)????? 5kg-m magnetic powder braking system:4 sets;
4)Rubber press-fit rollers:D200mm¡ÁL2000mm;
5)Quantity of rubber press-fit rollers:1set;
6)Pneumatic Level-off device;
7)Macromolecue film unwinding rollers:D100mm¡ÁL2000mm;
8)Quantity of macromolecue film unwinding rollers:2sets; |
1 |
|
7.Infrared-ray heating device |
1)Stainless steel reflecting cover;
2)S.C.R. electricity heat and power controlling system:4 sets;
3)Infrared ray heating power:100kw;
4)Cooling fan:0.55kw¡Á2sets; |
1 |
|
8.Heating rollers presetting composite device |
1)Steel chassis;
2)Aluminum panel guiding rollers:
a)Rollers with plate chrome:D200mm¡ÁL2000mm,2sets;
b)Rubber rollers:D300mm¡ÁL2000mm,2sets;
3)Heating roller composite device:
a)Composite rollers:made of special heat-resisting alloy with plate chrome treatment and high precise milling treatment;
b)Dimension:D450mm¡ÁL2000mm,6 sets;
c)High precise press-fit space adjusting device;
4)Driving device;
a)Straight axis reducer:1/500;
b)Driving parts and universal joint;
c)Driving motor:5kw-3phases-380v-50Hz(synchronized adjustable); |
1 |
|
9.Heating roller composite device |
1)Steel chassis;
2)Heating roller composite device:
a)Composite rollers:made of special heat-resisting alloy with plate chrome treatment and high precise milling treatment;
b)Dimension:D450mm¡ÁL2000mm,4 sets;
c)High precise press-fit space adjusting device;
d)D200mm pneumatic cylinder controlling device; |
1 |
Dimension:L2495mm¡ÁW1750mm¡ÁH2350mm; Weight: 6500kg; |
10.High precise roller composite device |
1)Steel chassis;
2)a)Composite rollers:made of special heat-resisting alloy with plate chrome treatment and high precise milling treatment;
b)Dimension:D450m¡ÁL2000mm,4 sets;
3)D200mm pneumatic cylinder and relative controlling device; ?
4)High precise press-fit space adjusting device;
5)Constant temperature heating system;
a)Forward roller heating power:36kw¡Á4kw¡Á1;
b)Heating medium:by water,24kw¡Á2.2kw¡Á1;
c)Temperature controlling system:adopt PID automatic system; |
1 |
|
11.Proportional controlling upside unreeling machine |
1) Weight of aluminum panel roller:5000kg;
2)Steel beam channel chassis;
3)63kg-m magnetic braking device;
4)Conic-shape holder driven by pneumatic cylinder;
5)Hydraulic cylinders for conic-shape holder;
6)Chassis position adjusting device;
7)Automatic proportional tensile-force controlling system; |
1 |
Dimension:L4140mm¡ÁW800mm¡ÁH1750mm; Weight:3500kg; |
12.Proportional controlling downside unreeling machine |
1)Weight of aluminum panel roller:5000kg;
2)Carbon steel beam channel chassis;
3)63kg-m magnetic braking device;
4)Chassis position adjusting device;
5)Hydraulic cylinders for conic-shape holder;
6)Chassis position adjusting device;
7)Automatic proportional tensile-force controlling system; |
1 |
|
13.Cooling device |
1)Dimension:L10000mm¡ÁW2470mm¡ÁH1800mm;
2)Carbon chassis;
3)Stove wall made of square pipe and high quality steel board;
4)Cooling fan:0.37kw¡Á32=11.84kw;
5)Holding rollers:adopt heat-proof and abrasion-proof rubber rollersD75mm¡ÁL2200mm;
6)Conveyer:adopt abrasion-proof rubber rollersD70mm¡Á6,2sets; |
1 |
|
14.Panel level-off machine with safeguard film coating device |
1)Carbon steel chassis;
2)Level-off rollers:made of special alloy with plate-chrome treatment;D160mm¡Á2200mm,5sets; ?
3)Down-depression device:driven by pneumatic cylinder;
4)Safeguard film bracket;
5)Rigid abrasion-proof rubber rollers:D160mm¡Á1800mm,1sets;
6) Macromolecule unwinding rollers: D100mm¡Á1800mm,1unit;
7)Pneumatic controlling parts; |
1 |
|
15.Constant-speed driving rollers |
1)Driving rollers:
a)D480mm¡ÁL2000mm, 2sets; abrasion-proof rubber rollers;
b)Pneumatic cylinder and auxiliary controlling parts;
c)Press-fit space adjusting device;
d)Driving parts:adopt universal joint;
e)Straight axis 1/400 reducer;
f)Driving motor:11kw(synchronized adjustable);
2)Rollers with constant-length sensors
a)Length encoder;
b)Rollers with plate-chrome treatment: D110mm¡Á2000mm,2sets;
c)Pneumatic cylinder and auxiliary controlling parts; |
1 |
|
16.Automatic cutting machine with adjustable- length device |
1)Carbon chassis;
2)Scissors both on the upside and downside;
3)Finger protection frame;
4)Hydraulic driving cylinder and auxiliary parts for scissors;
5)Hydraulic pump:5kw;
6)Pneumatic depression rollers;
7)Synchronized displacement pneumatic shaft;
8)Pneumatic auxiliary parts;
9)Electric controlling cabinet; |
1 |
Dimension:L2200mm¡ÁW820mm¡ÁH900mm; Weight:1500kg; Cutting capacity:ACP T6.0mm¡ÁL2000 |
17.Roller feeder |
|
1 |
|
18.Electric controlling cabinet |
1)Erect controlling cabinet;
2)Numeric temperature operation indication and controlling unit;
3)Speed adjusting device;
4)Switches for separated motors
5)Emergent-stop device;
6)Speed meters; |
1 |
|
19.Electricity power controlling cabinet |
1)Erect electric controlling cabinet;
2)Electricity power no-fuse switch;
3)Power contactor;
4)SCR controlling unit;
5)Current and voltage indication device;
6)Current and voltage split phase inspection switch; |
1 |
|
20.Warm-water controlling device of roller temperature |
1)Heating medium:constant warm water;
2)Heating method:flange-shape heater,
3)Heating power:12kw¡Á3unit=36kw;
4)Stainless steel water pump:1.5kw¡Á3;
5)3 point temperature controlling device;
6)Warning device for lack of water |
1 |
|
21.Diesel controlling device of roller temperature |
1)Electricity heating power:24kw¡Á10unit=240kw;
2)Heating temperature:¡Ü250¡æ;
3)Thermal medium swelling container;
4)Heat exchanger;
5)Heat recycling pump:1.5kw¡Á4=6kw;
6)Constant temperature heat exchange device;
7) Electric controlling device; |
1 |
|
22.Constant temperature heating system |
1)Forward roller heating medium:by recycling oil,36kw¡Á24kw¡Á1set;
2) Heating medium:by recycling water,24kw¡Á1.5kw¡Á1sets;
3)Temperature controlling system:adopt PID automatic system; |
1 |
|
23.Electricity power system |
1)Necessary voltage:380v¡À10%;
2)Necessary power:600kw; |
1 |
|
24.Compressed air system |
1)Capacity:0.9M3
2)Compressed air:7kg; |
1 |
|
25.Water system |
Capacity:15M3 |
1 |
|
Painting production line equipment
Categories: Painting production line equipment
product name: SC-FEA-1600£Ü2000
description:
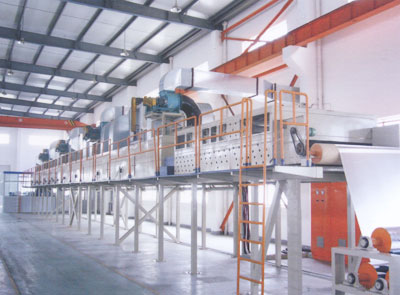

Aluminum coil sheet painting and stoving varnish equipment
functions:
1.?After surface anodization or formation treatment, aluminum alloy coil sheet turns into poriform film. Continuously roll all kinds of paint of different colors onto the film, after baking, film coated aluminum coil sheet with desired effect is obtained. This device has even color aberration in function. Tolerance of coated film is within 5um and the utilization rate of paint is above 96%.
2.?Through coil handling machine assorted with tension proportion control system, aluminum coil sheet is able to show out aluminum coil for degrease, neutralization, reduction and film switch treatment.
3.Precision coating machine employs reverse type coating method, spraying paint evenly onto the surface of aluminum coil sheet. Its rolling & painting wheel employs high precision steel tube, after grinding and hard plating, then applies precision grinding, with surface precision rate of within 0.003mm and straight drum rate of within 0.005mm.
Model: FEA-1600-AL15
Design Specification £º
Coating objective: aluminum or aluminum alloy coil sheet ¡¡Width: 910-1,600mm ¡¡Thickness: 0.08-0.60mm ¡¡Diameter of interior tube of coil sheet: ¦µ150-405mm
Dimension: 52,000L X 3,500W X 3,500H (mm)
Weight: 36,000kg (about)
Equipment component, shown as below
1.Tension control type convolving machine
Model: double-edged pyramid type push clamp
Weight of the coil: 3,000kg/p
Components: Iron sheet channel steel base
2.Splicer Function: splice evenly two aluminum coil ends on the splicer swiftly by employing high temperature adhesive tape.
Components: £¨1£©Iron sheet channel steel base ¡¡ £¨2£©Air pressure actuation type pressing component ¡¡
3.Roll painting precision hull coating machine
Function: this equipment employs rolling painting method¡ªpaint taking wheel takes paint from paint plat at the bottom of the stand, rolls to film securing wheel for certain paint according to paint thickness, then to painting wheel for surface painting of the aluminum plate. Roll painting wheel of this equipment is manufactured with high precision, able to evenly coat the surface of aluminum coil sheet and secure same painting quality of the sheet.
4.480kw recirculation stove varnish furnace
Model: channel type
Electric power: 480kw
Power supply: 3§æ-380V-50HZ Temperature: 150¡æ-260¡æ £¨MAX.270¡æ£© ?
5.Cooling Device
Model: fan cooling
Components: £¨1£©Stainless steel cooling section ¡¡£¨2£©Cooling coil ¡¡£¨3£©Water circulating pump ¡¡£¨4£©Cooling machine
6.Cooling roller train
Components:
£¨1£©Frame manufactured by steel plate cutting
£¨2£©Special heat-resistant alloy steel after chrome plating and precision grinding £¨3£©Swivel connection section used for cooling water passing in and out of rolling wheel
7.Constant speed driving roller train
Model: stepless speed regulating, constant speed drive Components: ¡¡£¨1£©Adjustable constant speed machine ¡¡£¨2£©director axis reducer ¡¡£¨3£©drive set ¡¡£¨4£©drive roller ¡¡£¨5£©Driven roller ¡¡£¨6£©Steering roller
8.Cutting worktable Components: ¡¡£¨1£©iron plate beam channel base ¡¡£¨2£©air-pressure pressing module ¡¡£¨3£©abrasion resistance rubber wheel
9.Oil pressure type automatic tracing adjustment device
Model: air pressure testing oil pressure driving Components: ¡¡£¨1£©Air pressure type testing inductor ¡¡£¨2£©Oil pressure pusher ¡¡£¨3£©Oil pressure control component ¡¡£¨4£©Full-automatic electric operating control box ¡¡£¨5£©Oil pressure pump engine
10.Automatic proportionate torque convolving machine
Model: double-edged pyramid type push clamp Components: £¨1£©iron sheet channel steel base ¡¡£¨2£©Automatic convolving torque machine ¡¡£¨3£©direct axis reducer ¡¡£¨4£©Push-type conical clamp ¡¡£¨5£©adjustable base device ¡¡£¨6£©Automatic proportionate torque control device
11.Electric output control box ¡¡¡¡Model: free standing ¡¡¡¡Structure: (1) free standing appliance box ¡¡£¨2£©Non-fuse switch ¡¡£¨3£©Motion contactor ¡¡£¨4£©Electric output S.C.R. control component ¡¡£¨5£©Current and voltage meter ¡¡£¨6£©Current and voltage phase splitting & switching check switch
12.Temperature control and operation control box ¡¡¡¡Structure: ¡¡¡¡(1) free standing control box ¡¡£¨2£©Numerical type temperature operation indicator and automatic control unit ¡¡£¨3£©Tension examination device ¡¡£¨4£©Speed regulation device ¡¡£¨5£©Operation indicator light ¡¡£¨6£©Temperature detector
13.Electric control box (torque wind-up control) ¡¡Structure ¡¡£¨1£©I I.C circuit control device ¡¡£¨2£©Tension set device ¡¡£¨3£©Tachometer ¡¡£¨4£©Operation button ¡¡£¨5£©Edge tracing control component
14. the coating mixes stirs the supplies installment Function explanation that?The paint fluid density mixes andstirs evenly Organization composition: (1) base steel frame (2) stirs adjusts the barrel trough (3) stirs the leaf blade, stirs the axis (4) paint fluid filtrating equipment(5) coating supplies diaphragm pump (6) coating transportation pipeline and pipe accessory (7) barometric pressure fluctuation trolley (8) the coating mixes the barrel Note: Equipment of the this unit table of contents, not including partas follows:
1 Installment, combination.
2 Public equipment: (1 )Supply source and so on water, electricity, compressed air (2) Running water, electricity, compressed air, by supply source toseller equipment on conveyance system: The electrical power box andbetween the electrical operation box matches the tube, the powerdistribution, the wind tube and its the related fitting. (Namely apower distribution,/two second wives manage project) (3)¡¡From seller equipment electricity power box and electrical operationbox to between seller equipment motor between, electric heating bodyand small operation box power distribution and its related fitting.(Namely two second wives electricity project) (4 )The circulation with the cooling tower, matches the tube and therelated fitting. (5) The gas discharges the pipeline and processes the facility. (6 )The painting sealed chamber, contains the fresh air to input thefacility, the waste gas discharges the facility and the airconditioning facility, (7 )painting sealed chamber operation. (8) After furnace body row of air blower exportation platoon wind tube,exhaust system fortification and its related fitting and so onrelaying row of air blower. (9) The cooling water cycle circuitry (contains water pump) (10 )The civil engineering contains the workshop and the equipmentfoundation. (11 )The installment, the test run, the production with the originalmaterial, the coating, the manpower, the tool, the hoisting,transports moves the facility, the examination, the experimentalinstrument and so on. (12 )The equipment revolution uses the lubricating oil 3. The seller supplies goods outside the scope other items.
|